Good Quality of Steel & Metal Working Technology
by Elaborate Machine Group Design Know-how
This line is Designed to produce all types of Single Skin or PU/PIR Insulated Panel.
It could be the most proper for the widest range of market needs.
Sheet Forming Line
Coil Car & Uncoiler
- Loading Capacity : 5, 7.5, 10, 12 ton
- Type : Hydraulic Mandrel Expanding & Mechanical Coil Guiding Type
- Drum Expending & Sliding Structure
- The Strongest Mechanical Design by Integral Structure
Leveller & Pre-Cutter
- Leveller : 4-High Type for Straightening the Steel Sheet Surface
- In Case of Higher Quality of Steel Sheet, It is not Necessary
- Chopper : Knife Cutting by Hydraulic / Pneumatic Power
- Steel Knife Materials : SKD 11
Protective Film Coater & Pinch Roller
- Protective Film Coater
- Roll Unrapping & Pressing Type by Synchronization
- Pinch Roller
- Double-Roll Side Guiding
- Material : SKD-11
Groove Patterning Roll Former
- Purpose : Different Panel Surface Shape for wide range of surface pattern while Avoiding Panel Surface Wave Problem
- Pattern Types : Wide Groove, Strip
- Steel Materials : S45C with Hard Chromium Coated Surface by Several Heat Treatment Process
- Type : Motorized Embossed Roll Pressing Type
Micro Wave Patterning Roll Former
- Purpose : Different Panel Surface Shape for wide range of surface pattern while Avoiding Panel Surface Wave Problem
- Pattern Types : Wide Groove, Strip, Several Kinds of Micro wave and the like
- Steel Materials : S45C with Hard Chromium Coated Surface by Several Heat Treatment Process
- Type : Motorized Roll Pressing Type
A-2.1. Rotary Embossing Press for Wood Grain Pattern
- Type : Roller Pressing Type
- Wedge Assembly : Side Pushing Wedge Jig by Screw, S45C
- Bearing Housing : S45C Box
- Bearing Caps : S45C
- GIBs : Upper Embossing Roll Housing
- Drive Connection : Female & Male Helical Gear Set
- Upper Roller Assembly : Φ300 × 900(L) mm, SACM1
- Lower Roller Assembly : Φ300 × 900(L) mm, SACM1 in High Frequency Heat Treatment
- Drive : AC Geared Motor Group
- Sensor : closed switch
- Main frame : welded steel structure
A-2.2. Rotary Embossing Press for Stucco Pattern
- Type : Roller Pressing Type
- Wedge Assembly : Side Pushing Wedge Jig by Screw, S45C
- Bearing Housing : S45C Box
- Bearing Caps : S45C
- GIBs : Upper Embossing Roll Housing
- Drive Connection : Female & Male Helical Gear Set
- Upper Roller Assembly : Φ300 × 900(L) mm, SACM1
- Lower Roller Assembly : Φ300 × 900(L) mm, SACM1 in High Frequency Heat Treatment
- Drive : AC Geared Motor Group
- Sensor : closed switch
- Main frame : welded steel structure
A-2.3. Precision Leveler
This unit is used for making flat surface of sheet from the process where upper rolls and lower rolls press up & down the continuous sheet from the uncoiling area,which in turn conveys the desired flat sheet into the sheet forming area.
- Type : Leveling by upper & lower roll pressing
- Roll dimension : 60mm × 900(L)
- Roll number : Upper : 5 ea, lower : 4 ea
- Speed : Max. 15m
- Roller materials : Hard chrome coated steel
- Drive : AC Geared Motor
- Leveling area : Max. 900mm
- Roll moving up & down : Air cylinder
A-3.1. Looping Sliding Conveyor
- Type : Height-adjustable stand type
- Roller : 20mm by Rubber Coated
- Roll Up/Down : 40 SPM in case of 400mm in pitch by Air Cylinder
A-3.2. NC Encoding Feeder
Feeding length is easily adjustable and feeding length & speed is synchronized with press machine.
Wrong-feeding detecting system is equipped in and height is adjustable.
- Type : Height-adjustable stand type
- Coil width : 900mm Max.
- Coil thickness : 0.3 ~ 1.0mm available
- Speed (adjustable) : 40 SPM in case of 400mm in pitch
- Release type : Air cylinder
- Drive : AC Servo motor 1.5~5.0Kw
A-3.3. Hydraulic Press
This hydraulic press is designed for embossing the surface of front door panel. This is installed synchronized with NC roll feeder and roll forming machine. Pressing power and speed are adjustable for exact planned performance.High speed performance is the main consideration for this press machine.
Simple-framed structure is made by hard steel. Individual control boxes and safe systems will guarantee the safety and work performance.
Automatic or manual manipulation is available. Digital pressure gauge, remote pressure controller and pressing timer are equipped.
Several safety systems such as laser detector, two-hand manipulation and safeguard block are equipped
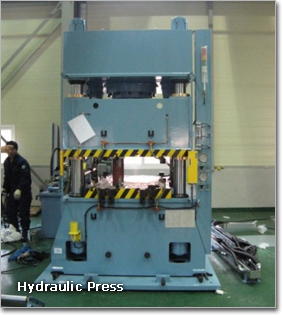
- Type : 4-Post hydraulic press
- Capacity : 250ton
- Cylinder : 560mm × 250mm stroke
- Open height : 600mm
- Speed : Adjustable
- Downward speed : 100mm/sec
- Pressing speed : 4mm/sec
- Ascending speed : 150mm/sec
- Service pressure : 210kg/cm2
- Bolster dimension : 1,000mm × 700mm
- Slide dimension : 1,000mm × 700mm
- Working dimension : 1,000mm(W) × 700mm(D)
- Tank capacity : 1,000 Liter
- Total dimension : 2,832mm(W) × 4,333mm(H) × 1,825mm(D)
- Control box : Digital switch pad type
A-3.4. Cassette Patterning Mould
- Materials : SKD11 & S45C
- Dimension : 600 × 400mm
- Set : 2 Sets
A-3.5. Spring Back Proof System
- Type : Die Cushion by Upward Supporting
- Dimension : 600 × 400mm
- Cylinder : 300mm
- Capacity : 100ton
A-4. Front Shearing Machine
This machine is used for the process of performing crosswise cutting on the steel sheet(coil). It is composed of a hydraulic cylinder powered knife that is designed to initially set the roll forming M/C and for regular or irregular production stop. It is also designed to cut without any need for stopping the production line.
- Type : Upper & Lower Knife cutting type
- Cutting speed : Max. 20 cuts/min
- Capacity : Max. 1.0mm(T) × 900mm(L)
- Drive : Hydraulic Cylinder
- knife : SKD-11
- Main frame : Welded steel structure
A-6. Coil In-feeding Facilities
This unit consists of a shearing unit, a side roller guide, a pinch roll, protective film coating unit and a supplementary side trimming device(Optional).
TradeBelt provides side trimming & corona device when buyer requires them.
This unit is commonly installed for both the upper and lower coils.(Corona treatment device is installed only for lower sheet to enhance the adhesive of Al sheet)
A-6.1. Side Guide
- Type : Left & Right Roll Guiding
- Drive : Idle
- Location Adjustment : By Handle
- Roller Materials : SCM21 in High Frequency Heat Treatment
A-6.2. Pinch Roller
A pinch roll is used to prevent the coil moving backwards, and to move it forwards by pinching coil (steel sheet).
- Type : Top roll lifting type
- Roller : 200mm × 900(L) - 2pcs (rubber coated)
- Top roll lifting : Air cylinder
- Drive : AC geared motor(1/10)
- Main body : welded steel structure
A-6.3. Protective Film Coating Device
This machine is designed for protecting panel skin by coating vinyl or other protective film while controlling tension of it.
A-7. Surface Patterning Roll Former
This machine is designed for Forming Different Panel Surface Shapes while Avoiding Panel Surface Wave Problem and improve Panel Outdoor Design.
- Type : Motorized Roll Pressing Type
- Pattern Types : Wide Groove , Strip & Microwave
- Stand : Cast Iron Steel
- Roller Stages : 2 stages for each pattern
- Roll Materials : SCM21 and Nickel-Chrome Coated in High Frequency Induction Hardening Heat Treatment Process
- Drive : AC Geared Motor with Inverter
A-8. Main Roll Former Group
There are Two Types of Roll Forming Process such as Post-Cutting after Roll Forming or Pre-Cutting before Roll Forming. Post-Cutting System needs a little bit higher Cost and larger Production Space than Pre-cutting System while Guaranteeing Better Quality of Panel in Surface and Side such as Waving and Curving Quality. TB Consortium Generally Recommends You to Apply Post-Cutting System with Continuous Steel Coil In-feeding in order to Prevent Panels from Curving and Waving Problems.
When we Start Your Project, We will get your Agreement on the Detailed Panel Drawings before Designing Our Roll Formers
Panel Type Exchange
There are two types of Roll Former Cassette Exchange such as Automatic Rail Traverse Type and Manually Overhead Crane Traverse Type.
TradeBelt
Roller Station
- Around 14 ~ 36 Stations depending on Panel Shape in Side & Surface
- Capped Joint or Interlock Joint Wall : about 12 Stations
- Trapezoidal Roof Roll Forming Machine : 24 Stations
- Concealed Joint Wall Roll Forming Machine : 22 Stations
- Check Pattern Wall Roll Forming Machine : 22 Stations
- Sinus Panel Roll Forming Machine : 24 Stations
- Siding Panel Roll Forming Machine : 22 Stations
- Small Sinus Panel Roll Forming Machine : 27 Stations
- Small Sharp Rib Panel Roll Forming Machine : 27 Stations
- Combined Siding Panel Roll Forming Machine : 24 Stations
- Driven by : Gear Box
- Roller Materials : SCM21
- Roller Surface : Hard Chromium Coating with Several Heat Treatment Process
- Roller Stand
- Cast Iron Set
- Dual Steel Plate Housing
- Single Steel Plate
Tiled Roof Roll Former
Tiled Roof Panel Production could be perfectly performed by Semi-Continuous or Discontinuous Production Mechanism, so that It requires independent roll forming line, which would let you produce single skin panel as well as PU/PIR Insulated Panel.
Tile Pattern Roll Former
- Roller Group : About 16 Stations
- Roller Materials : S45C
- Driven by : Gear & Chain by AC Inverter
Hydraulic Press for Widthwise Rib Pattern
- Capacity : about 10 ton (Changeable)
- Widthwise Movement : Inverter Drive with LM Guide
A-10.Post Cutting Press
Cutting the Shaped Panel into Necessary Panel Length in Hydraulic Press in Male & Female Mould while Guaranteeing Continuous Production as well as Wave-Proof and Curving-Proof.
- Male/Female Mould Materials : SKD 11
- Pressing Power depending on Panel Dimension
- Lengthwise movement in LM Guide by Servo Drive
A-11.Electric Control System (LG PLC System & Touch Screen Input)
This unit is commonly mounted in both the upper and lower Coil Forming.
The main control panel beside PU foaming unit can immediately controls the speed of the whole line when in manual mode.
Roll forming unit has the small manual-control panel for testing the roll forming unit’s operation.
- Type : stand box type by push button switch (pilot lamp)
- main control cabinet : 1 set
- operating panel: 1 set
- Electric Power : 380v 50Hz