TB-EKOSYSTEM Double Slat-Pressing Conveyor
- The Laminator is of high quality with design based on years of manufacturing experience and feedback from operating units. It is generally 30 meters long (centerline of sprocket to centerline of sprocket) isochronous chain-plate conveyors will basically be similarly constructed .
- The upper conveyor will be supported on electric cylinder lift and the guide units mounted on the lower conveyor. The frame of the conveyors will be of structural steel construction. The frames will be the frame cross-structures.
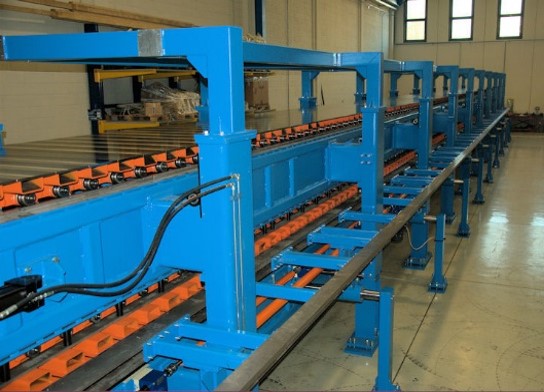
- The upper and lower belts are driven on head shafts mounted on anti-friction bearing and are equipped with take up units to maintain proper tension. The take up units will also compensate for thermal expansion and contraction.
- Trapezoidal jacks lift will raise and lower the upper conveyor to provide a gap of 30mm to 300mm between slat working surfaces. Vertical guides for the upper conveyor are provided.
- Horizontal distance between the two sides nylon seal blocks can be adjusted so can meet requirements of different width’s sandwich panel. The width is from 800mm to 1100mm.
TB-EKOSYSTEM HEATING AND INSULATION SYSTEM
- The heating system adopt exchanger heater, fan hot air to keep the temperature to 30-70 °C in the double belt machine.
- The temperature could adjust according to the production process.
- The laminator frames will be individually enclosed with double steel wall insulated panels sandwich panel.
- The plant will be supplied with two battery to heat and two battery to cool.
- The hot battery can work with hot cold or diathermic oil.
- The burner for hot water or diathermic oil is not included.
TB-EKOSYSTEM Continuous Cutting Machine
- The main carriage will then return to the home position for the next cutting cycle
- The cutting cycle can be initiated manually or by automatic length-cutting in conjunction with the central line system.
- This machinery is designed to cut panel during production of up to 1250 mm wide and up to 250mm thick.
- Cutting machine can move 2500mm longitudinally along product line;
- Band saw of the cutting machine can move transversely 1900mm, Cutting machine moves longitudinally and transversely along the slide way.
Cooling Conveyor
- To avoid the panel surface damage by PU foam post-reaction due to temperature difference
- Standard Conveying Length : max. 20,000mm
- Standard Conveying Cap. : max. 1,760m2
- In/Out-feeding : by PVC Belt Conveyor
- Drive : Cyclo Reducer
- Standard Available Cooling Time :
- max. 220 minutes in case of 8m/m in speed
- max. 290 minutes in case of 6m/m in speed
Stacking Line
- Turn-over : max. 9 sec by Cyclo Reducer
- Vacuum Pad : ¨ª120 with AL Block & Spring
- Power Transmitting by RS #80 chain
- Stacking Cycle : 16 sec.
- Main Drive : Rack Pinion Motor
- Vacuum Suction : by Vacuum Pump
Packing Line
- Lifted-Conveying : Lifted by Hydraulic Cylinder
- Lifted-Conveying Length : 1,350mm / 4sec
- Lifted-Conveying Cycle : 12 sec/cycle
- PP bending : Automatic Bending by Sensors
- Bending Cycle : 1.8 sec/rev
- Wrapping Wheel Diameter : ¨ª2,200 mm
- Recommended PE Wrap : 25¥ìm x 500mm
- Wrapping Speed : 3 m/sec
- Panel Conveying Speed : 10 m/min
- Drive : Cyclo Reducer